A lot has happened in the field of solar modules in recent decades, and thanks to new technologies, modules are becoming more powerful and durable. However, this also means that older modules can often no longer deliver the same performance. But there is now a solution for this, because it is possible to increase the electricity from modules produced before 2013/14 by means of an additional coating. Today, we will tell you all about this method.
The glass from PV modules manufactured before 2013/14 reflects more sunlight than later module series. As a result, they also produce less electricity than comparable modules produced after this period. Therefore, it is now possible to reduce reflection and make a change to the glass surface by means of an additional 140 nm thick silicon dioxide layer, thereby increasing current production by approx. 3-4%.
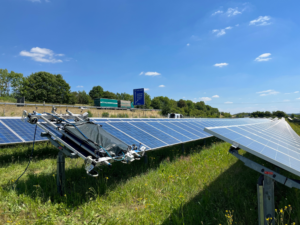
Coating at 35 degrees module temperature
The modules must first be made free from dirt before the silicon dioxide layer can be applied. For this purpose, the modules must have a temperature of at least 35 degrees. The coating is applied in liquid form, the silica is dissolved in alcohol, which then quickly evaporates due to the temperature during application. The coating remains behind, which changes the glass surface, thereby significantly reducing the reflection of sunlight. As the high temperature is required, application of the coating is weather dependent and can currently only be done between May and September. In addition, the technology is particularly well-suited to larger solar parks. Residential or commercial systems on roofs are not suitable for additional coating due to the accessibility of the modules.
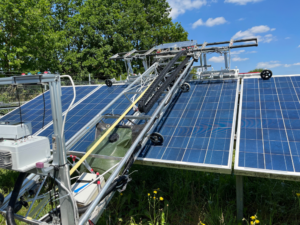
Is retrofitting worthwhile?
To illustrate how quickly upgrading older modules pays off, we have provided a small example: Solarpark Sukow GmbH & Co. KG from 2011, which has an annual energy production of 1,000 kWh/kWp and achieves 3% additional yield due to the coating, can expect 30 kWh/kWp more per year. This means that the upgrade will pay for itself in 3.5-4 years due to the cost.
There are currently no long-term experiences in the field that go beyond four years, only laboratory tests, but these are promising. The Fraunhofer Institute subjected the product to a number of complex tests, including a pressure cooker test, in which the coated modules are exposed to 130 °C/~3 bar for 30 minutes. This is an absolute hardness test for an additional coating and shows its durability. All the tests carried out produced good results, and none of the samples failed. The coating is expected to have a service life of over 20 years, which significantly enhances older modules over a long period of time.
So far, we have coated two IBC SOLAR solar parks and are very pleased with the results. Further systems are due to be coated this year. In the long term, we also want to offer this service to our Premium Partners. More about this soon here on our IBC SOLAR blog.